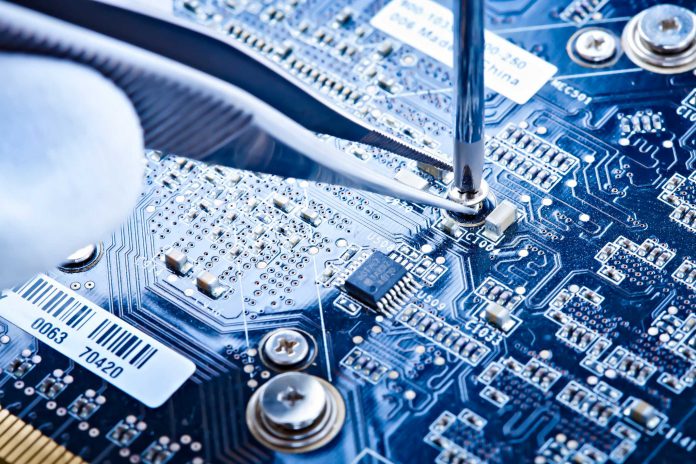
Several ways to comply with prescribed lockdown measures for supply chain sustainability have been shown in a study undertaken by Koncar et al in 2020, on Fast Moving Consumer Goods (FMCGs) during the Corona Virus Disease (COVID-19) pandemic in the Western Balkans region. The researchers purport that to ensure the smooth functioning of the FMGC supply chain, complete digitalization and automation of all business activities and operations must be based on the application of the Internet of Things (IoTs).
Indeed, supply chain disruptions emanating from the second wave of COVID-19 pandemic are beginning to negatively affect smooth operations in the Zambian manufacturing sector. Border closures are resurfacing to help curb the spread of the virus, and with restrictions on the movement of people and goods production line problems arising from the lack of manufacturing inputs which cannot be sourced locally, are re-emerging.
And so, with the current second wave of the pandemic manufacturing inputs are going to likely delay and if manufacturers cannot have their raw materials on time a serious threat remains on of scaling down production. Moreover, social distancing measures, intended to safeguard employees, mean that the entire labour force cannot work in the factory at the same time. The implication is that manufacturers have idle machinery and workers, making maximisation of asset utilisation a difficult task. The balance is in keeping in mind safety risks of employees whilst attaining production levels that allow for profitability and business continuity.
Despite these supply chain hurdles being faced by the manufacturing sector, there is a silver lining to the pandemic. The fourth industrial revolution presents opportunities and solutions as it has been said to blur the boundaries between the physical, digital and biological worlds. Deloitte and Touche in their 2020 report entitled ‘Internet of Things (IoT): The rise of the connected world” show that manufacturing modernisation has allowed for working digitally across locations and partner organisations by embracing the use of virtualisation.
Interestingly, through this concept, technological devices which are connected to the internet, can be embedded in the production line and be used to monitor critical production data remotely. Paolo Azzoni in his article, ‘Internet of Things in the Post Covid Era’, suggests that embracing this digital transformation and such new business models will allow for a quick recovery and ensure a leading position for the future.
How then can the IoTs be used to help the manufacturing sector recover post COVID-19 in Zambia?
As working from home has become a norm in Zambia, IoTs can also be used for industrial automation systems. The solution can ensure remote control of machinery in the production process whilst working from home. Supervisors not fully involved in the production process, can monitor quality and production while minimising their risk exposure to the virus and thus ensuring the safety of employees. Additionally, industrial automation can also ensure that the production process does not cease despite the absence of certain employees.
Besides, with current IoTs technology, it is possible to obtain real-time asset information and make informed decisions in the production process. The supply chain disruptions during the COVID-19 pandemic, caused by border restrictions, show the need of asset tracking of raw materials and finished goods. The IoT-based asset tracking system helps producers calculate the usage of manufacturing inputs, whilst initiating measures to shorten idle period and enhance utilization of the production process.
By using IoTs, high maintenance costs in the production process can also be avoided, as predictive repairing and maintenance can be undertaken. Essential maintenance data can be obtained from the production process including data to determine the state of the machinery, alert and warning sign transmissions and corresponding repair processes can be activated. Thus, production failure can be detected well in advance by the IoTs tools and help to transform equipment maintenance into a fast-paced and automated practice.
Furthermore, IoTs can use an approach called ‘Digital Twins’ to make physical copies of products manufactured by a company. Digital Twins allows a manufacturer to easily experiment and foresee the functionality, as well as initial and final operational capabilities of the product being developed. Therefore, in product development, IoTs are efficient, as data is used to refine the product till it is market ready. Moreover, IoTs tools can document product updates, predict potential issues and bottlenecks before a product goes on the production line.
Given the current situation, Covid 19 has only reinforced the need for the Zambian manufacturing sector to adopt smart technologies, such as IoTs in their production processes. The efficiency with which IoTs can be used to improve the production process and other tasks can significantly reduce production costs and increase incomes.
Nonetheless, for the manufacturing sector to fully utilise IoTs, telecommunications companies have to invest in internet infrastructure that can offer fast and reliable internet to support IoTs usage. Fifth Generation (5G) networks need to be quickly adopted in the country because they can handle IoTs due to its fast speed. Furthermore, telecommunications companies will need to work with the Government to ensure cheaper internet access so as to also allow micro, small and medium sized enterprises to utilise this technology.